以下是現場速記。
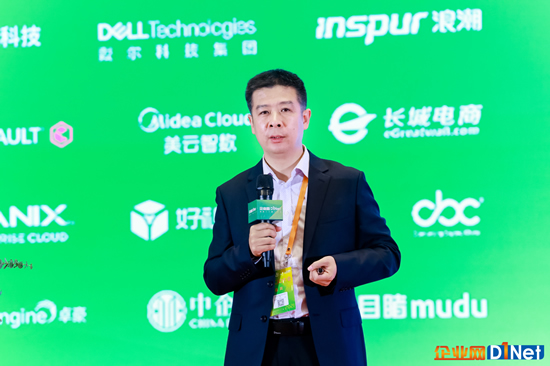
亞明汽車CIO 肖慶陽
肖慶陽:各位CIO的同仁們,大家下午好!聽了將近兩天的時間,感覺收獲不少,終于該輪到我了。
我接下來的分享可能是和之前的這些大佬們稍有一些不同的地方。因為我是來自于企業,在企業做了多年的CIO,所以說我們這個數字化轉型之路可能是更加的結合我們的實際公司生產經營。所以說希望通過我接下來的分享能夠給工業制造企業帶來一些啟發。有些觀點可能我們也可以相互的交流,進一步的交流、探討。
首先自我介紹一下我來自大連亞明汽車部件股份有限公司,在我們公司我也是一名老員工了。從事二十多年CIO的工作,一步步把企業從信息化為零開始一步步建設成國家級工業互聯網試點示范企業,在我們數字化轉型之路上我們也有很多的體會。接下來我會給大家進一步的交流!
首先給大家介紹企業背景。我們是一家傳統的汽車零部件生產的企業,產品下面會有介紹。亞明汽車近幾年來我們通過數字化轉型之路,我們承擔了一些國家級的科研項目,包括國家智能制造新模式項目,這是2017年。2018年國家重點研發計劃項目以及工業互聯網創新發展工程項目,在這些項目建設過程之中,我們為了完成國家任務在信息化上大力的進行投入,做了很多的工作。
通過20多年的數字化的建設,目前亞明汽車雖然說我們是一家小企業,但是在我們國內的同行業當中我們還是處于領先的水平,數字化程度還是比較高。
首先介紹一下公司,大連亞明汽車部件股份有限公司是一家以壓鑄件生產以及壓鑄模具設計與制造。我們公司有近70年的歷史。我們主要生產的產品是以汽車動力總成壓鑄件為主,像變速器、油底殼、鋼鐵、缸蓋這些零件,主要客戶是奔馳、大眾、福特等整車廠。近些年我們開始研發新能源三電產品。
這是我們客戶情況以及公司生產的產品,大家看我們的客戶都是一些頂級的國際上的汽車廠,包括我們現在最大的是豐田,第二是奔馳、大眾、福特,近些年我們又開發了像特斯拉以及沃爾沃新能源的汽車主機廠。
右邊是我們生產的零部件,大家看到是以鋁合金壓鑄件為主,它是鋁合金首先通過壓鑄工藝然后進行精加工。目前我們在新能源市場上呈增長的趨勢。
這個是我們即將建設新的工廠,大家看到我們有近70年的老廠房,這個廠房目前面積也非常小,已經無法適應我們下一步的企業發展。所以說我們在經濟開發區正在建設7萬多平的新工廠,新工廠主要以新能源汽車三電產品為主的生產。
對于企業來說,我們經過近些年的承接的國家項目以及數字化的轉型,目前已經初步形成了數字化、網絡化和智能化的生產模式。同時,亞明汽車也是中國國家亞洲前20強企業,也是國家零部件出口基地。目前我們也拿到了國家5G+工業互聯網第一批典型解決方案的提供商。
為什么我們會成為提供商?后面我會介紹,因為通過我們數字化轉型之路,我們現在也對外賦能,給其他的企業賦能來進行數字化的解決方案的提供。
數字化轉型的背景,通過這兩天跟許多大佬們一起分享、交流,大家其實對數字化轉型的趨勢以及企業的動力都已經談得非常透徹了。
我們的背景可能是有企業自身的發展原因,這里我也給大家分享一下。
首先我們是一家傳統的汽車零部件的供應商,作為一家汽車零部件的配套廠來講,我們的顧客就是主機廠。主機廠對我們有很苛刻的要求,大家看我列舉的主要的有三個:
第一個是準時交付。因為我們的客戶,你想他的奔馳、豐田生產線,每天根據生產計劃進行拉動生產,所以他絕對不允許出現停線的情況。我們作為配套的汽車零部件廠要求必須準時供貨,我們的生產計劃是一個滾動的計劃,大概每個月、每周甚至細化到每一天都有一個精確的交付的數量。這個對于我們來說是必須要給客戶保證的。
大家可能不知道如果由于我們的供貨出現對于客戶主機廠的停線,他會產生一個高額的索賠,大概一分鐘是2000塊錢,所以說風險非常大。
第二個他對品質的要求非常高,要求的是零缺陷。就是我們供給主機廠汽車零部件不允許有一件出問題,因為汽車關系到人民群眾生命財產的安全,我們誰也不希望我們在4S店買到的汽車在行駛的路上出現發動機的故障,所以這個對于質量的要求非常高。
另外對于年降。大家可能不太清楚這個詞,汽車主機廠要求我們所有零配件供應商每年要降價,而降價的幅度是由主機廠來提出的,就是這么霸道,沒有辦法。因為顧客就是我們的上帝。
所以說針對于這些來自于主機廠對汽車零部件、工廠的這樣的一些要求,作為零部件企業如何來應對?這也是我們最初搞數字化轉型我們的一個初衷和目標。
作為傳統的制造工廠來講,我想在座很多CIO都很清楚,我們制造工廠里面是一個什么樣的情況。大多數企業,在早些年都是缺少數據支撐,決策靠猜測這么樣一種情況,都是一種粗放式的靠人的經驗來主觀管理的情況,我們工廠在早些年也是這種情況。
那么怎么樣滿足客戶對于我們的要求?所以說你在這種情況下你就沒有辦法來滿足客戶的準時交付、零缺陷以及年降的要求。
這也是我們最早搞信息化也好、數字化也好的一個初衷。
這張PPT我想在座更多的是CIO,我是做過一段時間生產的部長以及生產的廠長。我非常清楚,在我們的工廠里,各個的部門、各個角色他們有哪些具體的痛點。
比如說像工藝、設備、生產的以及我們的一些高管,他都有他的管理上的問題和痛點。針對于這些問題,我們能不能用數字化、信息化的手段來解決這些問題?我想這也許是更加實實在在企業數字化轉型的一個總因。
隨著近年來我們國家也提出來數字化轉型將引領企業的未來,作為傳統的制造企業工廠,實際大多企業CIO已經越來越意識到數字化轉型是勢不可擋的,終于來了。實際上企業的領導者現在也認為,企業數字化轉型不是一道選擇題,而是一道生存題。
我們去年在寧波一些企業進行同行企業推廣我們解決方案時,有許多企業老板已經認識到這個層面了。企業不搞數字化確實是在等死,生存都存在問題,因為我們市場的變化,我們的客戶、我們的行業在日新月異的產生深刻的變革。
所以說這個也是我們大連亞明汽車在數字化轉型的一個初衷、動力。
接下來我跟大家再具體分享一下具體我們在轉型過程中我們的做法,我們是怎么來做的,我們為什么要做?可能我講述這些比較接地氣,比較實用。
大連亞明汽車數字化轉型發展歷程也跟大家介紹一下,實際我們搞數字化是非常早的。我們在1996年時,我們企業就成立了信息中心,當時信息中心的職能它還有一部分的三維設計,因為我們在96年的時候就已經搞了三維計算機輔助設計。還有一塊是信息化管理這一塊,我們ERP在2005年時就已經上了,是非常早的,到現在已經有15、16年的時間了。企業接觸信息化轉型還是比較早的。
在2007年時我們壓鑄車間,下面的圖是壓鑄生產已經實現了全自動化,不需要人,全部由機器人完成一個生產的過程。
在2010年我們的MES系統就已經上線,2017年我們又承接了國家智能制造的專項。
從以上發展歷程來看,作為汽車零部件配套企業,因為它有的時候也是被我們的客戶、我們的主機廠牽著走。2005年上ERP,因為我們作為福特的供應商必須具備數字化能力,銷售訂單必須和福特公司在網上進行EDI,它把訂單傳到ERP系統,我們發貨時通過發貨系統傳到福特工廠。所以汽車零部件企業數字化開展比較早。
這個是我們亞明汽車總體的智能制造方案的架構,大家看到我們也是從智能化的設計、裝備、制造以及經營這幾個方面來實現管理的優化、升級。
最終目標是讓制造企業搞數字化,還是實實在在的。我們的目標就是圍繞著增效、提質、降本這三個層面實實在在的來做的。最終通過增效、提質、降本來完成客戶對我們的要求,有對我們生產效率的提高、準時供貨以及對成本都有要求。
數字化轉型主要內容大概分九個方面:
第一個方面.引進了一些數字化和柔性化的自動化的生產線。
第二個方面.對一些老舊的生產設備進行智能化改造和數字化集成。
第三個方面.數字化關鍵技術制造的自主研發。
第四個方面.物聯網的建設與數據采集。
第五個方面.車間制造執行系統MES系統的建設。
第六個方面.基于5G視覺缺陷建設。
第七個方面.數字化生產管控平臺建設。
第八個方面.數字卵生與大數據應用。
第九個方面.AI工業檢測工具應用。
第一個方面是必須要滿足的,數字工廠已經不是靠幾臺車床就能完成的,我們現在全部是采用智能的壓鑄機以及智能機器人組成的,這個是重資產,投入非常大。
這里是我們壓鑄車間數字化裝備的建設,目前我們壓鑄的車間,有的同事可能不太清楚。我們生產是鋁合金壓鑄件,它需要噸位非常大的壓鑄機,整個壓鑄單元實現了壓鑄、切邊、碼垛、在線檢測全自動化的無人生產,這個是我們智能工廠的第一步,首先要花錢買設備,然后把它做集成。
有一個簡短的視頻,也是我們整個壓鑄單元生產的全過程,它通過自動的切邊、碼垛以及我們的AGV運輸,完成了無人化的全自動的生產。我們在數字化集成這個方面,我們通過自主研發的SCADA系統實現智能化監測和控制,通過在設備上加裝了很多傳感器,用于監測產品的品質。
像我們影響產品的關鍵指標:壓力和溫度,這些我們通過我們自主研發的采集系統,我們對于整個加工生產單元做了一個閉環的在線監測,實現實時控制。
右邊的是我們機臺的主要生產參數的看板。
這個是我們自主研發的壓鑄冷卻水可視化控制系統,獲得了大連市專利獎一等獎。我們加裝了大量傳感器包括溫度、流量傳感器,來對這些影響生產的主要的工藝參數進行監控。我們的數字化實際包括了管理的數字化和工藝的數字化,這個屬于工藝的數字化,它也是靠傳統。
以前當模具冷卻水出現故障時,往往是靠人去定期的巡檢,才能夠發現比如說溫度不夠或者壓力不夠。這個時候很容易形成批量的質量問題,讓企業受到很大的損失。這個項目也是我們IT部門和工藝部門聯合完成的。
大家看右邊通過IT的技術和OT的結合,我們就能夠不用人去點檢,隨時實時的對整個的模具生產狀態進行一個可視化的監測和控制。這樣最大程度上提高產品的品質、降低我們不良品的發生。
這個是我們機加工車間,目前有230臺套柔性加工設備以及我們的智能物流,我們現在全部把它設備、機臺全部聯網,實現了數據的實時采集。
這個是工業互聯網互聯互通的建設,目前工廠的設備層和我們的辦公網絡它實際上車間是兩套網絡,全部已經實現了數據的采集,包括工廠內部的人員、物料以及工藝、環境等等數據的采集我們都已經做了。
這個就是我們做的設備生產數據的采集與監控系統,大家看到上面是我們的設備商的PLC以及采集的模塊,以及我們后來自己加裝的傳感器。
大家有些工業企業的朋友可以看到我們生產的設備比較老舊,可能十幾、二十年的設備都有,怎么實現數字化的物聯?我們有時可以通過加裝傳感器,目前的傳感器品類比較多,溫度的、壓力的、流量的以及IO的采集的,實際上非常多,成本也不高。我們通過傳感器的加裝,就可以在下面實現設備的互聯互通。這些數據全部實時上傳到數據中心。海量的數據也可以進行工藝分析和優化,提高產品的品質。
另外最關鍵一點,有些設備如果出了問題,我們可以通過IT系統主動的推送報警來及時的發現,變被動的反應為主動的預防,這個是很重要的。
這里就比較容易了,我們通過對生產過程的數據采集,我們把人機料法環測這些數據通通打通,把它采集上來。大家可以看我們的人員,一卡通。從員工的考勤、就餐以及到車間的包工全部采用一張卡就把人的信息連到了網絡里面來。物料我們在有一些零部件上打印了激光的二維碼,像這個圖片是我們零件的二維碼。還有我們通過在周轉箱上張帖二維碼的方式完成掃碼入庫領料的操作。
我們原來ERP系統往往靠人工錄入單據,這樣數據滯后,而且數據不是很準確。通過掃碼的方式和ERP、MES系統打通,就實現了數據的及時采集,實現了物流和信息流的同步。
關于MES系統,我這兩天在吃飯的時候也聽見好多的CIO朋友在聊這個MES系統。這個MES系統確確實實因為它不是一個標準化的系統,可能每一家企業、每一個行業都不一樣,所以說實施MES的風險還是比較大的。
我們亞明汽車采用的是自主開發的方式,我們有自己的研發團隊,這些年我們在MES上主要還是自下而上的這么樣一種開發模式。我們從了解實際的業務需求,了解設備情況,了解工藝情況,所以說我們自己通過自主研發的方式構建了我們生產過程的一個MES系統,解決了我們的生產效率、產品質量和生產異常這樣的一些功能模塊。
用了效果還是比較好的,因為我們是自己給自己開發,給自己應用,我們會不斷的完善。目前很多同行到我們工廠來參觀的時候也比較看好我們這套系統,目前我們MES系統也已經推廣到我們的同行業的企業當中去。
這里是一個可視化的生產指揮中心,通過采集上來的這些設備數據、人員的數據以及物料以及工藝的數據,我們就可以來做可視化的生產管控中心。
大家看到我們做了非常多看板,這些看板全部在車間的現場。而且我們這個看板,大家可以看到,我們這個看板不是一個冷冰冰的大屏,我們是有人的。人可以在上面操作,看板實際上也是一個終端。
為什么要做這么多的看板?有一次我到我們的客戶-一汽豐田那里去參觀考察。當時令我非常震撼,因為一汽豐田車間廠房首先是5S做的特別好,它整個機加和壓鑄車間地面,當時我用手摸了一下,一點灰都沒有。日本企業做得非常好,但是百分之我非常詫異的是,不是很大的機加工車間有非常多的看板,當然它這個看板是傳統的紙制的,它用了很多卡片,每一天很多的工人去看板上做記錄。
所以當時座談會交流的時候我就問日本人,為什么豐田車間會有這么多的看板?工人干活同時還要經常到看板上去寫寫畫畫,我說這個是怎么考慮的?當時日本人給我的說法對我來說受益很大。他說看板不是給領導參觀看的,這個看板是我們發現問題和解決問題的一個平臺。們通過看板上的文字、表格、顏色我們就知道生產現場發生了什么,有哪些問題,應該誰來去解決?所以它實際是一個平臺和工具。
回來之后我們也做了大量的看板,大家可以看到我們看板上也有很多顏色、文字、進度條,而且這些看板在現場能夠一目了然,我們的車間管理者、領導還有工人、員工隨時隨地會看到我們生產過程當中異常的情況、設備的情況、工藝的情況。效果還是非常好的。
這里我們也是跟豐田學習了安燈的系統,一汽豐田主要采用的是安燈系統。我們自己開發做了改良,系統也是和我們機臺全部聯網,當機臺發生異常時候,我們傳感器探測出設備,比如說有機械故障或者是電器故障的時候,首先它會自動的采集到這個狀態。
如果是說這里有復雜的問題,我們通過員工在現場的呼叫,它就會自動的給我們運維人員發送手機的短信或者直接會撥打一個電話。這樣,我們的運維人員會及時的處置提高生產效率。
像我們重資產企業我們生產設備要求24小時不停機,因為我們要保證產量,保證交付能力,設備運維是非常重要的。以往設備出問題時往往處置時間會非常長,尤其信息也不透明,這樣對現場的執行力是很不夠的。上了這個安燈系統之后,我們大大的有效的提高了現場的執行力。
這套系統用的也是非常的好。我們在物料這一塊,在物料流轉這一塊,大家知道ERP系統它有物料入出庫功能。昨天我還和一位CIO朋友在聊,我說你們這個ERP系統帳物相符嗎?入庫單準嗎?他說有部分時間段是準的。作為汽車零部件來講我們每天是拉動式生產,必須確保賬物相符,我們采用打碼、掃碼方式直接和ERP系統同步,保證物料、領料、入庫和系統和實物是同步的。
簡單介紹一下這個,通過引進兩臺AGV車,完成壓鑄車間到物料的實時配送。
這個是我們的生產指揮中心,我們的系統現在實現了管理駕駛艙的功能。這個是在手機端、移動端,我們也實現了信息的主動的推送。
這個是一個車間的數字卵生系統,在我們產品生產車間,左邊是虛擬產線,右邊是物理產線,這個車間是黑燈車間,平時沒有人。所以我們運維人員可以在監控室里面看到車間生產運營情況。
這個是我們基于5GAI視覺檢測系統,我們通過在現場安裝工業相機對零部件進行拍攝,拍攝完之后會把數據通過5G,通過在云端進行比對。
對于數字化轉型的效益來講,從提質增效降本,對于企業競爭力的提升作用還是非常明顯的。
我們現在數字化解決方案,我們也專門成立了一個研發的團隊,我們現在數字化解決方案給同行業進行賦能。我們最近在2021年時也對外簽訂了1千多萬元的訂單,用我們這個數字化研究成果目前對外進入復制和推廣階段。
對于數字化轉型有五點體會:
首先是企業領導者依然要有戰略的決心來做這個事兒。
第二以人為中心。我們說企業里面實際上看似一套冰冷的系統,實際上它是和人是密不可分的,我們只有提高我們的員工的整體意識,對數字化轉型的認識,它才能夠起到比較好的效果。
再有業務流程的再造,實現一個數據去驅動決策,這個我想CIO們大家都有一定共識。
最后一個敢于試錯,持續改進。
數字化轉型大家都已經達成共識,它是勢不可擋的趨勢。數字化轉型對企業來講,像我們企業經過實踐來講我們覺得它不是一蹴而就的。對于我們來講我們要有這方面的認識,我們仍然還需要不斷的探索,不斷的創新,來把我們數字化轉型越做越好
我的分享就到這兒,謝謝大家!