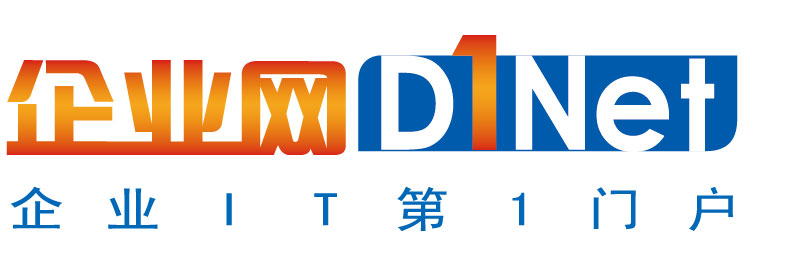

新松機器人自動化股份公司總裁助理 劉長勇
今天我分享的題目是從機器人到智能制造,之所以選擇這個題目,正是反映了新松公司發展的一個歷程,因為新松公司是從做機器人的開始,發展到現在能提供智能制造解決方案的一個公司。
今天的分享分為三個部分,第一個相關技術背景的介紹。第二部分是新松公司為客戶做的一些數字化車間的案例,和我們自己用的數字化車間的一個案例。最后是新松關于這方面和未來趨勢的一些觀點。
首先簡單回顧一下機器人發展史,機器人的發展史分為三個階段,第一階段從1920年—1948年,這是一個理論積累的階段,從機器人概念的提出到機器人三原則。在1942年由阿西莫夫也是在科幻小說中提出了機器人三定律,也是目前我們遵守的三定律。1948年出版的《控制論》,主要講的是控制方法的論述,為機器人誕生奠定了堅定的理論基礎。
到80年代日本由于大力發展汽車工業,工業機器人在日本首先取得了大量的應用和迅速發展,日本成為工業機器人的王國。直到現在第三階段,由于復雜工況的發展,特別是人工智能的發展,智能機器人越來越成為機器人的發展趨勢,包括最近幾年出現的服務機器人越來越得到了應用。特別是2015年有些專家把它叫做服務機器人的發展元年,將來的機器人肯定是向數字化、網絡化發展的。
中國機器人直到70年代末才發展起來,我們的老首長,中國科學院沈陽自動化研究所蔣新松院士,頂著巨大壓力提出來發展中國工業機器人,因為當時的普遍觀點是中國的勞動力很多,不需要發展機器人。后來首先在中科院沈陽自動化研究所就開展了這方面技術和應用的研究,接著在哈爾濱工業大學等各個大學都做了很多研究。在七五期間國家投資在中國科學院沈陽自動化研究所建立了中國的一個國家工程機器人研究中心,后來發展成為新松公司。
機器人發展史上我們得到了兩點啟示,一個是機器人概念的提出。大家注意到機器人概念包括它的三原則,都不是從事這方面的工程師和科學家提出來了,而是由科幻作家提出來了。我們分析為什么?就因為當時實現這個技術沒有得到發展,被科幻作家他當時不會考慮到怎么樣實現,他只需要有這個需求,幻想能想出來。這就是說我們智能制造也好,也會成為這方面的限制,要求我們必須跳出這個框框,產生很多新奇的想法,才能將來更有跨越式的發展。
第二,工業機器人的普及。是由美國發明的,但是當時并沒有在美國取得迅速的普及,而是由日本普及,這是一個機遇的問題,同時也是一個真正的需求問題。任何一個應用技術的發展,離不開兩個因素,一個是需求因素,另外一個是支撐因素。只有達到這兩個因素,任何一項新技術才能得到迅猛的發展和普及。
在分享案例之前我先簡單介紹一下新松公司,新松公司2000年以前是中科院沈陽自動化研究所的研究部,后來趕上當時中科院的知識創新工程,主旨是能夠產業化的技術要拿出來產業化,就以這個為契機成立了新松公司。我們的老首長蔣新松院士1997年去世,當時英國人把他叫中國機器人之父。2009年在創業板第一批上市,為新松注入了很大的活力和動力。我們的股票就叫機器人,后來在金融市場形成了機器人概念的板塊,現在還有四五十家和機器人概念相關的上市公司。
目前新松公司機器人有兩大類,一類是工業機器人,一類是服務機器人。即將推向市場的是醫療輔助機器人,比如說陪護機器人,養老的智能床。 公司有2500多家,70%是設計研發人員,因為我們公司80%、90%產品都是給客戶量身定制的,所以需要大量技術人員。
新松的數字化車間也和大家得差不多,我想任何一個制造業歸納起來無非就是說把能源、燃料和人機、設備投入進去,經過生產過程產出兩種,一種是我們要的產品,一種是排放。我們的目的是生產出最好的,滿足我們個性需要的產品,把排放降到最低。新松公司的數字化車間管理管控系統,實際上也可以叫做MES,是信息技術和工業技術的融合。
另外一個就是能源管理,怎么能把它的排放,包括污染的排放和能源消耗降到最低,這是我們在生產過程中要立即執行目標,它的手段有透明化、生產管理、智能決策,依賴職能裝備實現這個目標。
我分享一下我們在不同行業的案例,這是汽車行業的案例,工藝很簡單,這條生產系統分為兩個系統,前面一個系統生產的東西是汽車載體,大家看到汽車尾氣當中有一個加粗的部分,實際上就是這個圓形的東西,有的是陶瓷載體,有的是不銹鋼載體。這個工藝系統把要配配制的東西均勻涂在小孔當中,其實工藝很簡單。但是大家看到原來最早的傳統工藝是通過一個高壓擠壓把這個從一端擠到另一端出來為止,但是過程當中涂了多少它不知道。因為這個如果要說涂的太多,發動機產生廢氣會有堵塞影響發動機的效率。如果涂的太少,這個廢氣通過這個孔的時候氧化還原反應不充分,就達不到排放標準。這種如果涂的不多或者不均勻,會產生很多廢氣達不到國家的排放標準。
我們怎么解決這個問題的?因為這是一個標準生產的問題,首先我們是把數據都采集出來,比如說在載體涂之前,一定得出來它的涂量,再用功能模塊來分析它的走勢,然后再反饋智能裝備里頭來調整它,這樣根據它的預測結果就不會產生廢品。我們在正確當中大家都知道防措有三種,最高級的防措是不產生差錯,因為它沒有廢品出現。最不好的是最不接受差錯,現在我們做到了不產生差錯,在過程中根據軟件的預判結合智能裝備,實現了不產生差錯。
第二個,整個生產線在生產完之后有一個檢測,過去大家看到這邊這個,過去是靠人眼,他照射過去靠人觀察,目測檢查透光率。人工檢查一致性很差,人情緒都有關系,如果他情緒不好容易產生誤判,傳到汽車廠容易產生很大損失。我們采用了一個裝置,采用曲線分析和數據采集比對,得到了一個當量的在線檢查方法。大家會問為什么不用離線的設備?因為它的節拍和條件都不允許在線使用,只有我們數據比對的方法采用在線,滿足了節拍要求又滿足了生產監控的要求。
另外一個就是能源的問題,涂之后要經過爐的升溫,過去傳統方式是采用一個恒溫爐全部進去。它這個蒸發現象不是說溫度越高越好,會有一個曲線,我們就根據這個曲線,根據爐溫的變化,這樣一個提高了它的蒸發效率,另外節省能源。采用這種方法比原來的方法節省能源50%,因為這種是電加熱,非常耗能源。這是我們生產設備的整個結構,我們整個管理層包括設備的可視化。
我接著分享另外一個案例。這是為蘋果做芯片的一個公司,大家看到這個機床都是它原有的,是國外產的,并且有十幾道工序。過去每個工序之間是通過人來搬運,大家知道一個里頭的東西價值30萬,在搬運過程中經常發生危險磕碰,造成很大損失。目前采用49臺復合機器人,把整個機床連起來,上面有一個管理系統或者叫MES系統,和倉庫連接起來,當訂單通過ERP下達的時候,會分解到包括機床等系統,形成一個互聯,所有的狀態,包括設備之間連接,整個實現了無人化的車間。
大家看到整個生產系統,所有的件從外邊入庫之后實現了計算機的管理追溯,這邊是表示入料區,所有的全入倉庫,這邊實行了計算機的管理。包括機器人管理的系統,上面有一個MES系統,和原來的ERP相連。當訂單下來的時候,由MES系統分解到每個系統,然后它會自動出庫,根據計劃和下達的任務分解到每個工序上去,由機器人執行自動裝配。有些需要清洗的送到自動清洗室去清洗。
我想最后說兩句話,就是關于機器人的。將來的機器人肯定是網絡化、數字化發展,并且是人機共享,才能滿足信息化的發展。
謝謝大家。
