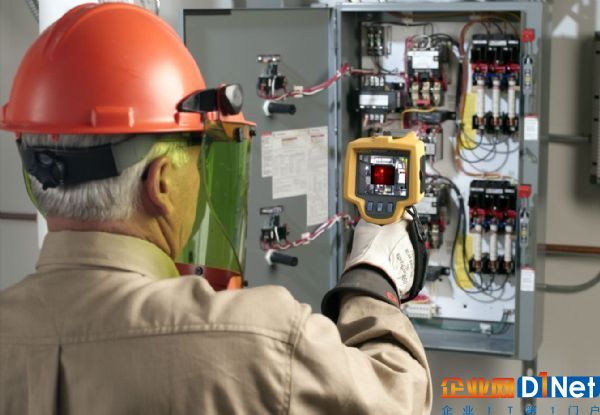
工業4.0提供新的技術,可以量化停機時間,并監測、預測故障。Fluke
機器故障讓制造業付出巨額成本,所幸現在的傳感器與機器學習等新技術,可以做到提前預測,進而減少停機時間。據Bureau of Analysis數據,美國平均工業設備使用年限,從1970年代以后就持續拉長,現在平均的使用時間都已達到10年。隨著資產老化,故障與維修的機會就變得越來越多。
物聯網預測性維修業者Presenso共同創辦人暨執行官Eitan Vesely表示,目前許多制造業者仍采用到故障為止(Run-to-failure)的方式,這種被動式的維修,但這其實要付出昂貴的成本,除了維修故障的機器之外,這還會損害整個生產線。
由于制造機器的年限持續拉長,制造業者復出的成本與風險也跟著上升。許多公司并未精確量化他們的停機成本,但據估計,就算是小型工廠,其每小時產生的成本也可能高達數萬美元。
工業4.0提供新的技術,可以量化停機時間,并監測、預測故障。機器中的傳感器,可以透過先進的算法,快速顯示出異常的趨勢與問題。
一般人工方式需要拿著清單,并設定許多變數,并根據歷史數據進行評估;機器有復雜的演法,可以考慮成千上萬個變量,而且實時偵測出細微的改變,這是傳統方法作不到的。
Infosys全球調查指出,盡管81%制造商明白機器學習有助于機器維修,但只有17%真正采用了相關技術。許多中小型業者還在使用1980年代的系統,甚至使用人工的數據分析。
還沒導入預測性分析的制造業者可能會問,究竟這么做的投資報酬率有多高?使用預測性分析,需要投資傳感器和SaaS解決方案等。制造業者應該了解相關分析工具的精準度,同時考慮停機所造成的沖擊,然后做出綜合評估。
Vesley認為,一開始應該從概念驗證開始,如果能夠提前偵測出資產故障,這時候管理階層就比較容易接受這樣的提議。跨部門的合作,包括IT部門與營運部門的整合,也是非常重要。