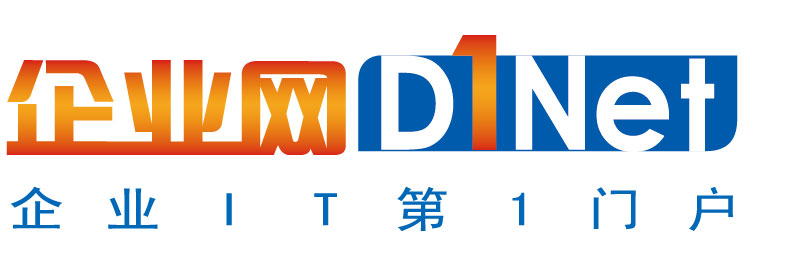
煉油和化工行業是是典型的流程型生產模式,工藝過程高度依賴設備的長期、穩定、安全和高效運行。因此,設備維護對煉油化工企業至關重要,任何一臺關鍵設備的故障停機都可能導致數以百萬甚至千萬級的經濟損失。
設備維護分為預防性維護、預知性維護和事后維護。流程型行業的特點決定了對于非關鍵類的設備可以采取事后維修的方式,以降低維護成本;對于關鍵類的設備必須采取預防性維護和預知性維護相結合的方式,保證設備能夠長期可靠運行。對于預防性維護,通常利用3年到4年一次的生產裝置大修機會對設備進行解體維修。在設備運行期間,主要依靠每月的計劃維護工作開對設備進行預知性維護。
目前在中國石化北京燕山分公司制定月度維護計劃的依據主要是設備管理人員的經驗,現場設備運行過程中表現出來的故障現象,以及公司規定的強制保養項目。我們知道,人為經驗是有局限性的,是缺乏繼承性的,這就導致了企業的維護計劃不能夠完全滿足設備安全可靠運行的要求,“過修”和“失修”情況并存。而如何能夠利用設備運行狀態數據,通過數據分析、數據挖掘等技術制定科學合理的檢修維護計劃,成為企業急需要解決的問題。另一方面,當設備出現運行異常情況時,如何能夠通過對其狀態數據的分析判斷進而在設備真正發生故障之前能夠捕捉到設備的故障征兆,為提前安排停車檢修爭取到更長的時間,也是企業一直面臨的難題。提前發現設備故障,提前進行生產計劃調整和物資準備,就意味著減少非計劃停車時間,進而為企業避免數額巨大的經濟損失。
面對燕山石化提出的問題,極晨智道提出應用大數據技術結合振動分析技術為企業建設設備全生命周期預知維修系統解決方案。由燕山石化、極晨智道和上海星環科技三家單位組建聯合項目組,歷經1年半的技術開發和現場實施服務,系統成功上線并達到預期的效果。
設備全生命周期預知維修系統從現場設備狀態監測系統和實時數據庫系統中獲取軸承振動、溫度、壓力、流量等數據。大型機組主要在線采集軸瓦位移的時域波形數據和溫度數據,數據采集周期為3-5秒;機泵以在線或離線方式采集振動速度或加速度數據和溫度數據,在線監測方式的數據采集周期為1小時,離線監測方式的數據采集周期為1-7天;系統從實時數據庫系統中獲取設備所對應的工藝參數,包括壓力、溫度、流量、液位、介質組分等等,數據采集周期為1-5秒。依據該數據采集策略和中石化集團的設備總量,預計數據規??梢赃_到1-5PB/年。利用傳統的關系型數據庫已經無法處理如此大規模的數據,所以在該項目中引入了上海星環的大數據平臺作為數據獲取、轉換和計算平臺。
設備全生命周期預知維修系統構建了基于規則的故障診斷、基于案例的故障診斷、設備狀態劣化趨勢預測、部件剩余壽命預測等應用?;谝巹t的故障診斷利用了經典診斷分析技術和專家系統理論,通過對所獲取的數據進行故障征兆提取,再依據診斷規則,自動輸出設備將要或已經發生的故障情況以及處理措施;基于案例的故障診斷功能在系統中構建了案例模型,并且從企業歷史故障記錄中提煉總結了若干故障案例作為原案例保存在大數據平臺中,設備當前運行狀態作為目標案例實時與原案例進行相似度計算,當相似度達到預設值時,系統給出與設備當前狀態相似的歷史故障案例及相似度;劣化趨勢預測功能應用大數據平臺中提供的若干算法,包括聚類、分類、回歸、神經網絡、灰度模型等,對所采集到的數據進行分析預測,系統自動給出設備所處的狀態類別和參數達到報警的時間;劣化趨勢預測功能還引入了自適應報警的概念,通過自適應報警算法模型進行計算,系統能夠針對每個設備的每個測點給出符合當前工況的報警閾值,當然這種自適應報警閾值一定是在符合相關企業和國家標準的前提下才能發揮其作用;部件剩余壽命預測功能利用設備啟停和歷史部件更換信息以及設備故障診斷和預測結果,系統通過計算得到部件的剩余壽命并對小于預設值的部件進行報警提醒。
燕山石化目前的數據量約為1000萬條/天,每年的數據規模達到20-30TB。設備全生命周期預知維修系統利用5臺服務器組成的集群部署了星環大數據平臺,包括內存計算、Hbase和流處理模塊。系統架構如下圖所示。
利用星環大數據平臺,系統實現了對數據的實時分析計算,使設備故障診斷和趨勢預測等功能的延遲控制在5秒之內,完全滿足的客戶對實時性的要求;通過對各類數據的分析,顛覆了傳統中人們的經驗思維,看似很多無關的數據,但卻對設備故障產生著實實在在的影響,例如設備運行效率過低時設備故障發生的概率增大,這就要求做好工藝參數控制;利用大數據分析自動生成的檢修維護計劃,保證了設備維護更有針對性,減少了“過修”和“失修”現象;大數據分析最有價值之處在于能夠在設備出現故障隱患時就發現設備的潛在故障,大大減少了生成裝置的非計劃停車,從經濟方面和安全方面為企業帶了了巨大的價值。下圖為系統自動給出的故障診斷結論:
設備全生命周期預知維修系統在國內乃至國際上首次將大數據技術應用到流程型生產行業的設備診斷和預測中,取得了初步成效,但仍有很多業務和技術問題需要進行攻關。例如,如何利用數據挖掘技術自動創建故障征兆算法,使系統更具智能性,拜托故障診斷專家的支持;如何利用進行大數據的預處理,并且是這種預處理模型化,讓系統自動完成;如何在對設備劣化趨勢進行預測時能夠結合失效機理的因素,使得預測的結果更加符合客觀現實等等。這些問題需要數據科學家、故障診斷專家和設備管理專業人員共同攻關解決,希望通過各類專業人員的努力,讓設備全生命周期預知維修系統發揮出更大的價值,徹底解決企業設備管理人員所面臨的種種難題,讓設備管理不再是企業中“費力不討好”的工作。