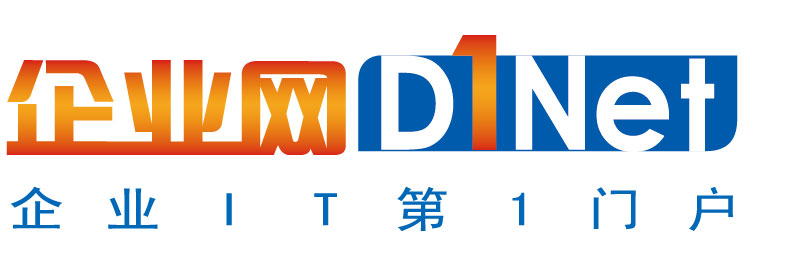
艾普工華 市場&咨詢部總監 楊凱
“十三五”時期是我國制造業提質增效、由大變強的關鍵期。智能轉型是建設制造強國的關鍵,實現“數字化、網絡化、智能化”制造,是制造業發展的新趨勢,也是新一輪科技革命和產業變革的核心所在。當前中國智能制造產業尚處于初級發展期,大部分企業處于起步階段。以電子行業為例,最大EMS的企業富士康,已于2015年開始逐步加快“機器換人”的步伐,海信、格力等家電制造企業也在自動化生產線上下足了功夫。諸如此類,多數企業的智能制造依然在初級階段,但是由此帶來的成本效益卻是顯而易見的。
目前,國內制造企業推進智能制造建設如火如荼,企業逐步開始在“智能研發”、“智能物流”、“智能生產”、“智能管理”、“智能服務”、“智能產品”、“智能裝備”這七個方面嘗試推進相關應用,有的企業關注“轉型升級”,有的企業關注“提質增效”。
通過國家統計局的官網,我看到了在2016年,全國規模以上工業企業實現利潤總額68803.2億元,比上年增長8.5%。2017年1-4月份,規模以上工業企業利潤總額同比增長24.4% ,增速比1-3 月份放緩 3.9 個百分點;其中,4月份利潤增長14%。工業利潤增速放緩,是前期高位增長后的合理回歸。總體看,目前工業利潤仍保持良好增長態勢。這應該也是大多數企業目前推進智能制造的應用效果。也給目前處在觀望或者等待的企業,增強了信心。
制造企業推進“提質增效”,目的就是要有效控制各項成本,提高生產效率,提升技術、質量和服務水平,創新發展空間,提升市場競爭能力。為此,制造企業應該建立相關的推進團隊和機制,引導企業各個部門降本增效、創新生產經營模式增效、市場開拓增效、戰略轉型增效,全面管理和控制生產經營成本,積極延伸產業鏈,拓展發展新空間,變革生產經營模式,加快推進創業創新,提高戰略應變能力和風險防控能力,全面促進和保障企業提質增效。結合自身的實際情況,找準制約提質增效的短板和瓶頸問題,積極與國內外領先企業進行全面對標,明確差距和提升方向,制定有針對性的主要路徑進行突破,切實提升發展質量、增加效益。但是,要明確一點,路徑規劃一定要清晰,不要貪大求全,要逐一擊破、分步實施。大家應該很清楚,生產環節的六要素(人、機、料、法、環、測)和六目標(效率、品質、成本、交期、土氣、安全)是管理工作的重點,提質增效依然是圍繞六要素和六目標進行推進。
1、提質量
產品質量的影響因素貫穿與產品的整個生命周期,必須收集、監控和分析整個產品周期從研發、采購、制造、質保、銷售及客戶服務等過程的質量信息。制造企業必須建立有效的質量數據采集機制,全過程采集六要素中的質量相關信息,最大限度地保證質量數據的及時性、準確性和全面性,構建產品質量數據中心。更為重要的是要利用好產品質量數據中心的數據,挖掘其中的價值,不僅是簡單地做個分析,而是要通過分析發現問題,進而制定監管和改善措施,并組織實施。接下來進入新一輪的PDCA循環:質量數據收集—數據分析—發現問題—制定改善措施、組織實施,如此循環往復。在一次次的循環中,企業不斷地加強質量問題的監督管理,切實做到產品質量的不斷提升。
從產品研發設計開始,到整個生產過程乃至投入市場使用,完善的產品數字化檔案,不僅可以保證產品數據的完整性,也可在此基礎上實現設計制造一體化,實現制造過程中以預防為主,監控為輔,分析改善為有效手段的質量管控體系。
另外,不要讓企業現有的質量工程和管理體系成為文檔服務器上的一份份文件,而是要成為真正指導企業提升產品質量的指導性文件,實現質量人員從“事后補救”到“事前預防”的職能轉變,從而增強企業自身的核心競爭力。
2、增效率
在生產環節提高生產效率,依然從六要素來分析生產環節中存在的問題:
人:員工工作技能較低(員工技能考核機制滯后),缺乏有效的技能培訓;班組長管理能力不足,未做到因材施用,督導功能缺失;缺少合理的激勵機制,團隊工作積極性不高,士氣低落、缺乏責任心、效率意識薄弱。
機:生產使用設備及夾治具缺乏標準化維護和保養要求,無專人負責管理,臺賬、狀態、使用記錄、點檢保養記錄、維修記錄等基礎信息缺失,部分設備及夾治具缺少操作指引,造成員工操作不當,嚴重影響生產效率。
料:未建立明確可行的物料采購、倉儲、運輸、質檢等方面的管理制度;對外購原材料、半成品、成品未進行批次或序列管理;對過程中的可疑品、不合格品未建立有效控制辦法;生產過程中物料信息采集依靠紙質單據,效率較低,且不利于物料追溯。
法:部分產品生產流程設計及作業方法不合理,導致生產過程不連續,效率低下;SOP缺乏實用性,員工操作方法未標準化;新產品及久未生產產品缺少工程技術指導,異常較多,處理不及時,返工耗費大量工時;生產安排、排線不合理,平衡損失大,等待浪費多。
環:生產現場規劃混亂,5S管理落后,物料及工具無定置管理,現場目視化缺失,造成員工尋找和拿取物料及工具時的時間浪費。
測:針對檢驗規范標準化較低,大量的手工填寫內容。檢測報告需要人工整理。無論是自檢、互檢還是專檢,僅僅是按照標準進行記錄,沒有發揮檢驗的真實價值。
這六個方面的效率提升,有的是需要提升管理,有的需要引入信息化系統來配合管理提升效率,有的需要進行精益生產規劃和改善。
3、降成本
我相信很多企業已經推進了全面預算、戰略成本理念、目標成本管理、資金周轉管理、強化成本核算、建立成本責任制度等等完善的成本管理和控制體系,但是,從技術角度來解決成本較高的問題,還需找到可以優化的成本增高點。
制造企業的成本來源就是制造一定種類產品和數量所支出的各種費用之和,成本因素貫穿制造活動的全生命周期,生產成本分為直接成本(原材料費用、工人工資等)和間接成本(管理費用、折舊費用、維修費用、機物料消耗費用等)。另外,還包括一個質量成本,這些都是實實在在能夠數據化和分析的成本結構。
直接成本,常規就是通過產品設計改進和生產工藝改進,降低消耗定額來降成本。
間接成本,常規就是加強費用的預算管理,提高各單元的費用控制粒度來降成本。
質量成本,常規就是從產品原料、制程、工藝三個方面來嚴格控制降低造成不良的質量成本。
對于制造企業來說,無論是工藝改進,還是機器換人,或者是提高管控粒度,都是一個重要的課題,例如:
在鑄造企業,熔化環節,通過改造設備,提高煤氣的燃燒利用率,降低消耗定額。
在設備管控環節,通過設備狀態數據采集及大數據分析,優化設備維修保養的頻次和備件的使用壽命,降低成本。
對于員工的工資,分析低技術含量、操作頻次較高的可以使用機器取代人的工作崗位,優化人員結構,提高作業效率和精度,從而降低成本。
采用計件工資的企業,對計劃的合理性、計件報工數據的真實性、時效性要進行監控,以最優的任務,最準確的數據核算成本。
在噴涂車間,對噴涂計劃和交付計劃優化排程,以最低的油漆浪費和人力浪費,降低成本。
以繼電器生產為例,以一次性投入的自動化裝配、測試、封裝設備來代替傳統手工作業,初步建立“無人化工廠”,應對國內日益增高的人工成本;
通過設備數據采集與質量數據分析等手段,實時監控產品生產工藝參數,降低不良品的產生;
通過生產過程的數字化管理手段,降低生產業務過程中的人工、時間成本。
……
智能制造的本質,是將智能裝備(包括但不限于機器人、數控機床、自動化集成裝備、3D打印等)通過通信技術有機連接起來,實現生產過程自動化,優化生產工藝,提高生產效率;并通過各類感知技術(傳感器、RFID、機器視覺等)收集生產過程中的各種數據,通過工業以太網等通信手段,上傳至工業服務器,在MES軟件系統的管理下進行數據處理分析,并與企業資源管理軟件(ERP)對接,提供最優化的生產方案或者定制化生產,最終實現智能化生產;研發創新智能產品,為企業在新的市場環境中,打造新的商業模式,建立新的業務價值增長點。讓提質增效的路徑更加清晰,執行更加透明,決策更加科學,效果更加明顯。