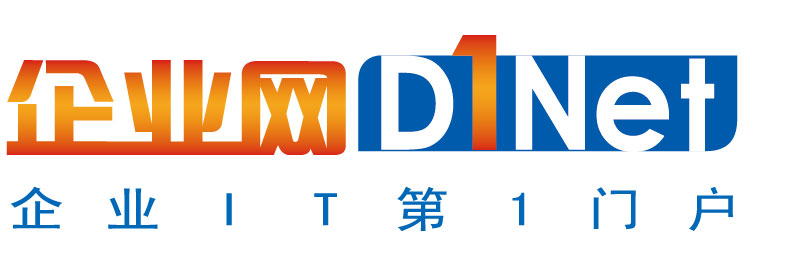
總在微信朋友圈里看到紅領集團CIO米慶洋發的定制西裝美照,版型富于設計,立體感極強,關鍵是:著裝人非常合身,精神氣立顯。這,可能就是定制服裝的魅力吧!
創辦于1995年的紅領,2008年之前只是一家服裝公司,這樣的服裝公司在中國以十萬起計。但從2008年開始,紅領開始轉型做個性化定制,用信息化驅動個性化定制模式,已形成了明顯的經濟效益。米慶洋說:“紅領已成為中國傳統企業向互聯網轉型的樣板企業,從2015年到現在,每年都有四、五十家企業老板去紅領參觀學習,希望在中國的現狀下能找到一個出路。”
傳統企業的轉型之路有著極強的內因與外因,中國的土地成本以及人員工資的增加,導致大量美國或歐洲的公司的工廠轉移到東南亞,中國世界工廠的地位直線下滑,與此對應的,中國的制造業產能過剩現象非常嚴重。紅領轉型定制化后,庫存幾乎沒有壓力,且利潤基本實現了年年往上增長,訂單量穩步超長。基于此,紅領從2015年10月份專門成立了一家科技公司,以幫助傳統行業轉型升級。
企業網D1Net將從信息化角度為大家解讀紅領的轉型之路。
紅領集團CIO米慶洋
紅領的信息化到底有何不同?
紅領的信息化和別的公司的信息化有什么不同呢?比如:前幾天筆者曾在一家做家具的工廠參觀,它的物料從進廠到出廠整個過程是不落地的,但是定制的時候就出了問題,按照自動化流程,每月訂單的處理應該在15天之內可以出貨,但是在生產線流轉的過程是兩個月都出不來。也就是設備自動化只能解決現場物流的情況,以及替代人工的東西可以實現自動化,但是在訂單處理過程中,每一個訂單的BOM都是不一樣的,沒辦法通過自動化設備處理,只能通過數據的自動匹配解決這個問題。
如何解決上述問題,德國工業4.0也曾探索過。但德國工業4.0講究的是設備智能化,比如生產某個零件,大家都用同樣的標準。紅領甚至超越了德國工業4.0嗎?
米慶洋說:“紅領信息化內部叫工業4.5,是通過數據的智能化來實現定制。舉個例子,如果沒有系統支撐和流水線的話,一般流程是訂單下達之后,由板師把訂單轉化成標準的板或者標準工藝,但定制企業最難的問題是,沒有那么多的板師和工藝員。怎么辦?紅領通過多年積累的經驗,把所有的數據累積到數據庫,讓系統自動的處理相關的數據,完成板師和工藝員的工作。訂單下達到車間,整個過程都是自動的,從用戶數據的收集到訂單信息,到產品的開發,到工藝規劃,到生產制造,數據的處理過程是自動,只有制造過程有工人。”
紅領智慧工廠之演變
紅領智慧工廠發展的歷程經歷了四步:
第一步,傳統工廠;
第二步,上了訂單系統和MES系統,做到了無紙化辦公;
第三步,實現了數據工廠間的融合,主要在于解決工廠返修率過高的問題,2010年,紅領研發人員和技術人員已達到了100多人,發現每天的訂單返修率200%,每件衣服必須在車間內返修兩次才能出廠,解決的辦法是把數據全部融進去,讓數據模擬工藝員和板師應考慮的問題,經過兩年的探索,紅領形成了支撐個性化定制,提升工業化效率的整個架構。
第四步,實現了一個平臺統一管理。個性化定制的特點是在款式顏色尺碼做了模塊化的擴展,脫離了傳統的款色碼編碼的管理,通過模塊化的管理形成數據庫。紅領基于三個層面:自組織、自覺察、自維護,把人、物和機器運轉起來,讓大家在一個平臺上處理相關的問題。目前紅領整個生產過程是7天,基本上做到了按小時方式下單。
紅領智慧工廠技術架構揭密
紅領智慧工廠以互聯網思維進行業務創新,創新的背后,需要強大IT支撐能力的同時,也需要企業IT的經營能力,讓軟件的生產、交互、獲取、升級、遙測變得更加簡單。在當今時代,這也被稱之為數字化轉型。據全球IT權威機構IDC的調查顯示,目前64%的企業已經成為數字化轉型的探索者和實踐者,全球“財富100強”企業將在今年底前完成數字化改造計劃的制定。然而,未知的技術欠債、過高的隱性成本、失真的知識傳遞、缺乏架構的支持等問題時刻阻礙著企業的數字化轉型。當前人類生活已經進入虛擬時空和現實時空交織一體的階段,大軟件、大應用難以適應快速變化的環境,而只有微服務架構才能夠提高應用、管理、交付、運維的整體效率,實現數字化時代的企業敏捷。
正是從應用的視角出發,紅領對于借助物聯網、互聯網、云計算技術,全面打通從客戶端(C端)到制造端(M端)的業務流程,解決個性化定制帶來的生產不確定性、多樣性和復雜性問題,實現全面、高效個性化定制交付(C2M)起到了決定性作用。