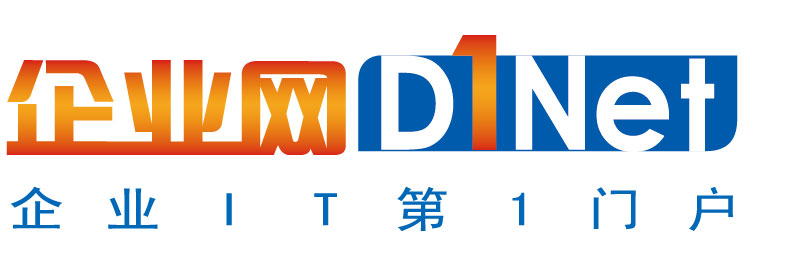
答案是肯定的,就是一個甲方目標清晰,顧問給力、項目管控良好的ERP項目既能降低節省人力又能提升各項管理指標。
但是事實上,有很多的ERP項目陷入了混亂,不僅沒有達到提升管理指標的目的,而且又浪費了大量的人力物力,我舉一個我2007年實施過的項目作為例子說明,該制造廠是一個生產拖拉機的企業,在上這個項目之前,實施過一套baan的ERP系統,失敗以后又重新找了我們,這次目標很清晰:就是降低庫存、提升準時交付率。
1、我們實施的第一件事情就是整理物料編碼、搭建bom(物料清單)。為什么要做這項工作呢?因為象拖拉機制造這類離散制造行業,管理面對的最大一個挑戰就是保證在庫存最低的情況下按時生產出所需要的貨物,最好是需要的零件一到立刻就被安裝到產品上(如果做不好,就會出現倉庫積壓大量的呆滯材料、生產線旁邊堆積著因缺少1種材料而無法完工的產品,客戶跳腳大罵銷售經理為什么不按時交貨、銷售和生產天天吵架等各種亂象)。要做到這點實在是太難了,下面的圖表示的是一個非常簡單的產品t的物料需求計劃,有興趣的同學可以手工算一下需要多長時間,也可以研究一下用excel是否能夠計算出來。再考慮一下如果有上百種t產品,每個t產品下有幾千種零部件用excel是否能夠計算出來(還要考慮倉庫的結存量、訂貨未到量、已經安排生產計劃未領用數量等等)。
ERP系統中的一個MRP模塊就是做這項工作的工具,但是使用好這個工具的前提是你要有準確的物料清單(BOM)和唯一的物料編碼,這是達成這個目標的前提。
我的這個項目前期baan系統實施時,就是和“無知”答主描寫的一樣,“后來實在整不過來了,就找了好多實習學生,生吞活剝的編制上了,以后工程師只作新圖紙的BOM,勉強可以應付來。”甲方也吸取了經驗教訓,組織產品設計部門花費了很多時間,其中的艱辛不必多表,總之終于整理出來相對準確的物資編碼和物料清單。
2、你以為整理出來物料編碼和bom就可以高枕無憂了嗎?當然不是。這個企業以前一直使用“領料制”,即車間配備領料員,缺什么東西都要拿著領料單到倉庫去領用材料。我們在方案中建議客戶把“領料制”變更為“配送制”即將車間的領料員收歸倉庫進行管理,因為ERP系統中已經有生產訂單和用料計劃,倉庫就可以知道“何時把何種材料送到何地”,沒有必要像以前一樣由領料員看看車間哪項材料缺乏,然后去倉庫領料。但是討論方案的時候大家各種不理解,最后好在客戶方總經理是個明白人力主進行此項變革。當然后來所有人都愛上了這個配送制。
3、還有一些其他事情,比如材料結算。以前供應商都是持自己的入庫單到倉庫送貨,供應商保留其中一欄到月底附發票到財務報賬。自從上了系統以后,材料會計就總抱怨結算工作量太大:要一逐個核對供應商的入庫單和系統中錄入的入庫單是否一致,然后根據入庫單在系統中錄入發票,中間要不間斷的來回折騰對賬,簡直要死了。后來根據我們的建議更改了流程:每到月底,材料會計在系統中分供應商打印出供應商的材料出庫單明細交供應商作為開票依據,供應商發票來了以后直接錄入就ok了。不僅解決了工作量問題,而且提前知道了本月應付賬款數據,供應商也不用來回折騰,大家皆大歡喜。
整體來講,就像開一輛suv,你在崎嶇的路上使用“雪地模式”覺得還好,但是你到高速公路上還使用“雪地模式”那你就要憤怒了。記住:ERP系統上線后,你腳下的路已經變了,所以你必須要找到更適合的走路方式。