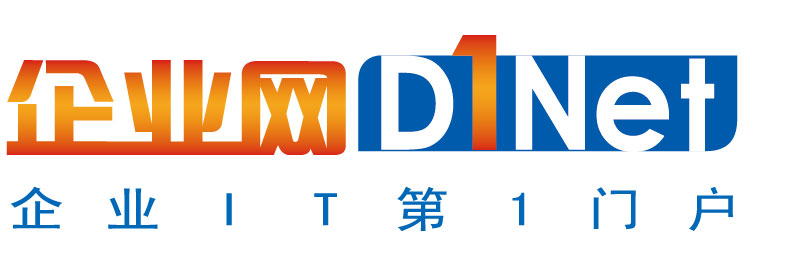
從設備資產(chǎn)效益產(chǎn)出角度看,我國制造業(yè)的設備綜合效率的提升空間巨大。據(jù)統(tǒng)計,我國大部分離散制造業(yè)的OEE在60%左右,距離發(fā)達國家至少還有10%-20%的提升空間。同時,很多工廠對設備維護和保養(yǎng)的精細化管理不夠重視,這當中造成的異常停機和備件浪費等隱性損失,更是巨大的浪費。在當前疫情沖擊、全球化局勢不確定性進一步增加的形勢下,這些效益改善空間,都可以為企業(yè)的生存、增強競爭力提供寶貴的機會。
圖:離散制造業(yè)OEE現(xiàn)狀評估
如何構建面向新型設備的管理能力,是當前制造業(yè)面臨的一個問題和挑戰(zhàn)。在這個過程中,我們總結了大家常常存在的5個誤區(qū),并給出了對應的策略建議,希望可以幫助企業(yè)少走一些彎路。
第一,重硬輕軟
大部分企業(yè)新建工廠或者新購買的設備,只重視硬件的驗收交接,忽視了軟件的維護保養(yǎng)、校準標準,沒有明確要求設備數(shù)據(jù)采集接口和設備數(shù)據(jù)所有權的訴求。根據(jù)工信部相關數(shù)據(jù)最新統(tǒng)計,目前我國企業(yè)生產(chǎn)設備的數(shù)字化率平均為47%,關鍵工藝的數(shù)控化率51%,關鍵設備聯(lián)網(wǎng)率41%。 嵌入式軟件、人機界面、數(shù)據(jù)監(jiān)測模型、管理平臺都是新型設備的重要組成部分,都應是新型設備管理的范疇。從筆者進行工業(yè)互聯(lián)網(wǎng)相關項目的經(jīng)驗看,設備的數(shù)據(jù)采集受制于工業(yè)現(xiàn)場協(xié)議眾多、原廠不開放不支持、設備數(shù)據(jù)不確權等原因,設備數(shù)采仍然是生產(chǎn)現(xiàn)場數(shù)字化推進中成本最高的組成部分之一。比如我國許多SMT產(chǎn)線,貼片機本身精度很高、節(jié)拍很快、良率也都在99%以上了,單純再靠手工調試,很難再提升了。許多工廠期望能將貼片機的數(shù)據(jù)實時數(shù)采和分析,解決自動叫料接料問題,改善拋料問題。但目前動輒數(shù)萬的數(shù)采license費用,讓許多工廠望而卻步。
因此,工廠在設備采購環(huán)節(jié)就提前考慮,將相關要求加入商務條款,可以為以后設備制程詳細數(shù)據(jù)的采集和分析優(yōu)化做好準備。
第二,生產(chǎn)為重,不壞不修、不停不管
在大部分工廠,特別是離散制造業(yè),都是生產(chǎn)是老大,設備只是保障部門,只要還能運轉,就不會停產(chǎn),這導致設備維護改善的時間和資金投入嚴重不足,設備部也陷入了四處救火、窮于應付的被動惡性循環(huán)。究其原因,是因為沒有從工廠端到端視角看設備停機的損失。在設備初期征兆的時候介入維護,遠比造成停機后再維護,造成的損失和投入成本要小的多。如下圖,某機床通過振動分析,可以看到10月18日振動加速度峰值觸發(fā)早期預警閾值,但是由于生產(chǎn)計劃問題,沒有停機維護;10月22日機床主控系統(tǒng)觸發(fā)故障,不得不停機過10個小時維修和更換軸承,維修后,振動恢復正常水平,但巨大損失已經(jīng)造成。
圖:通過振動分析可以監(jiān)測大部分機械故障
從設備管理大體經(jīng)過的4個主要階段來看,從1.0的糾正性維護(CM),到2.0預防性維護(PM)、3.0的可靠性維護(RCM)、4.0的預測性維護(PHM),本質上都是以設備健康管理(EHM)為中心,從“治已病”到“治未病”的進化過程。通過EHM,設備健康狀態(tài)不再是被簡單的劃分為正常、異常。我們可以通過新技術、新工具,分析積累的基礎數(shù)據(jù),評估出設備的亞健康狀態(tài),此時提前介入可以大大減少設備維護成本。例如,東智EHM給設備維護工程師配備帶有振動傳感器的智能點檢儀,就像給醫(yī)生配了“智能聽診器”一樣,通過數(shù)秒的監(jiān)測振動頻譜,結合內置的頻譜分析模型,就可以準確、快速的判斷出設備健康狀態(tài)、故障征兆原因,對故障輔助診斷起到重大作用。這樣設備人的職責從原來的壞了維修,更多的轉向如何保障設備健康運行的專業(yè)維保維護工作,進入良性循環(huán)。
第三,設備問題就是設備部的事情
雖然TPM已經(jīng)推行了多年,但許多管理者觀念和行動上,還是認為設備出了問題,就是設備部的事情,導致生產(chǎn)部門對設備的故障不關心,對影響產(chǎn)量、質量的設備維護不重視。設備維護工程師也往往低地位、低薪酬,自嘲為看門狗和替罪羊:節(jié)假日,別人可以休息,他們卻不能離開,因為這正是維修設備的好時機;凡是出了問題,無論是設備停機,生產(chǎn)停產(chǎn),還是質量事故,都會與設備相關,設備人員幾乎永遠是背鍋的。為此,整個設備部成了優(yōu)秀的人最不愿意去的地方。這種惡性循環(huán)現(xiàn)象,需要生產(chǎn)管理者身體力行樹立正確的設備管理理念,構建生產(chǎn)為主體的全員自主維保體系。只有生產(chǎn)部門管理者重視起來了,全體生產(chǎn)設備操作者才能改變對設備漠不關心的態(tài)度,才能有效進行設備保養(yǎng)。而這個光靠設備部是玩不轉的。
工廠可以通過引入設備健康管理EHM解決方案,構建全員自主維護保養(yǎng)體系,實現(xiàn)操作工的日常自主點檢和保養(yǎng)、設備部的專業(yè)點檢、設備故障掃碼報修、掃碼維護、維保工單自主搶單、維修效果用戶評價、績效競比等功能和機制,幫助工廠實現(xiàn)TPM的自運轉。
第四,將設備維護當做成本中心,忽視了冰山下的損失
許多管理者認為設備零故障是不可實現(xiàn)的,企業(yè)在遇到困難需要削減成本時,很多情況是拿設備維修費用開刀,甚至提出讓維修預算每年遞減百分之幾的目標。從傳統(tǒng)財務角度看,維修所消耗的資金一般被定義為成本和費用。其實早在30年前,德國召開歐洲維修團體聯(lián)盟國際會議時,就提出“維修——為了未來的投資“的主題。作為投資,就需要有清晰的投入產(chǎn)出。維修的投入是設備日常維護所投入的人工費、各類防護費、備件費、設備管理相關系統(tǒng)。產(chǎn)出是什么呢?是由于設備維護不足、設備管理不善,帶來的設備停機、精度或者質量缺陷帶來的損失。如果對這些損失的價值誤判,則容易扼殺設備維護技術和管理體系的改善性投入。
筆者曾經(jīng)服務過一家大型工廠,設備部要上馬EHM項目,實現(xiàn)設備的數(shù)據(jù)采集和監(jiān)控,同時通過移動化的巡點檢,實現(xiàn)設備的報修和維護過程,形成設備的故障樹記錄。在核算投入產(chǎn)出的時候,屢屢被財務挑戰(zhàn),過不了關。他們理解降低設備停機1小時的價值,僅僅是這1小時涉及到的員工的人工成本。這樣算下來,價值產(chǎn)出太低,許多設備改善項目沒法上馬。而且這樣的項目價值核算標準,直接打壓了工廠精益革新的積極性。設備停機一小時的損失,要從工廠視角端到端的去衡量整體,這里面其實包括了產(chǎn)能損失的機會成本,即1小時的產(chǎn)品產(chǎn)值損失,才是這個工廠真正的損失。這樣算下來,工廠許多可以改善停機、改善浪費、現(xiàn)場精益類的小改小革的項目,都可以得到了合理的開展,能激發(fā)起基層員工的創(chuàng)新積極性,也確實能給工廠帶來實實在在的效益。
在實際操作中還存在一個問題,就是備件的更換很大程度上掌握在維修工手上,存在著許多“人為掌握”更換的因素。維修人員大都靠經(jīng)驗判別備件損壞程度,對懷疑有故障的零部件,通常為了減少背責、或降低工作難度,即使還可以用也會更換成新的,可能存在過度維護的隱性浪費。比如在TCL華星光電,由于大部分都是進口件,每年備件費用就數(shù)億,通過東智設備健康管理EHM,構建精細化的備件生命周期管理,通過數(shù)據(jù)追蹤備件的實際可運行周期,每年可節(jié)省數(shù)千萬的成本。
從以上這些視角看,設備維護工作由過去的強調為生產(chǎn)服務,追求較高的設備完好率指標轉變到以企業(yè)的經(jīng)濟效益為中心,要求設備管理工作重視維修費用的管理與控制,找到以最少的維修費用達到最高的設備可利用率的平衡點。企業(yè)的高層管理者如果能夠從“投資”的角度認識維修和設備管理,將是十分寶貴的管理創(chuàng)新和理念轉變。
圖:設備管理的本質是找到最佳維護平衡點
第五,想依賴“預測性維護”解決問題,忽視了基礎的數(shù)字化建設和數(shù)據(jù)積累
“預測性維護”一直是工業(yè)互聯(lián)網(wǎng)的熱門話題,聲稱通過物聯(lián)網(wǎng)和AI實現(xiàn)了預測性維護的公司繁多,工廠也期望將自己對設備故障的不確定性,交給 “預測性維護”來解決。但據(jù)筆者觀察,目前大部分此類項目仍是概念和實驗性的居多,在可解釋性,可驗證性、可復制性上都有問題。
預測性維護的落地比預想中困難,是因為企圖單純依賴數(shù)據(jù)提取可解釋的工業(yè)機理邏輯,難度遠超想象。這里主要兩個原因:一是因為許多企業(yè)的基礎數(shù)據(jù)還缺乏積累,比如設備基本的巡點檢、維護保養(yǎng)、故障分析記錄,都還是散落在各種紙張、Excel中,設備缺乏數(shù)字化檔案,基本維護保養(yǎng)數(shù)據(jù)、備件更換記錄、故障和修理數(shù)據(jù),包括設備的故障特征數(shù)據(jù)還沒有結構化的積累,就不可能實現(xiàn)模型的訓練和驗證。二是許多廠商企圖單純得依賴數(shù)據(jù)分析路徑而忽略了設備工程師現(xiàn)有專業(yè)知識和經(jīng)驗的融入,光靠數(shù)學和AI算法容易走入統(tǒng)計陷阱,只是得到了相關性模型,不容易得出可解釋的因果性的預測模型。
總的來看,設備之于工廠,就像槍之于戰(zhàn)士。許多設備維護維修技術體系,也確實是從軍隊武器維護體系發(fā)展來的。構建新型的設備管理能力,需要工廠管理者,認識到設備之于工廠核心競爭力的基礎性,積極變革促使設備管理和作業(yè)方式,向數(shù)字化、智能化發(fā)展。根據(jù)Gartner預測,到2022年,60%以上的設備,將實現(xiàn)基于數(shù)據(jù)的智能運維方式,設備智能化管理和運維能力將會是衡量一個工廠核心競爭力的重要標志。最近國家工信部相關部門也正在起草和制定設備管理的國家標準、能力成熟度評估框架,將會對指導企業(yè)加強新型設備管理能力起到指引和促進作用。