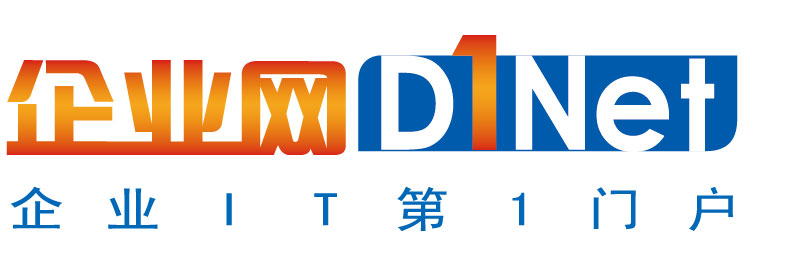
新華報業網訊 10月30日召開的國務院常務會議,通過《深化“互聯網+先進制造業”發展工業互聯網的指導意見》,要求加快建設和發展工業互聯網,促進新一代信息技術與制造業深度融合,推動實體經濟轉型升級。
近年來,全球工業互聯網發展駛入快車道,成為新一輪產業變革的關鍵驅動力量。江蘇搶抓先機,去年制定實施企業互聯網提升計劃,推動企業開展新模式、新制造、新業態創新實踐,涌現出一批“互聯網+先進制造業”典型,制造業生態悄然改變。互聯網到底如何“讓制造更聰明”?記者采訪江蘇省內多家先行先試企業。
模式1:打造智能化車間實現提質增效
友達光電(昆山)有限公司,是一家專業生產第六代低溫多晶硅液晶面板的臺資企業。借助工業互聯網,該公司打造的數字化管理車間,通過對生產過程中各類數據的采集、分析、利用,實現對生產全過程的全數字化管理和實時可視化管控。友達光電工廠負責人介紹,目前企業的主要機臺設備都已加裝新型傳感器,實現數據的實時回收。通過友達內部建制的專業工業大數據分析平臺,進行挖掘、分析找出參數關聯關系,快速解決生產異常,提升生產效率。
“生產過程中,各制程產生的關鍵產品參數達數百項,生產機臺的運行參數也有數千項,這些參數的累計變異非常多。異常發生時,通過使用大數據分析軟件可提升準確性,有利于企業提升效率,提升良品率,降低成本。”這位負責人舉例說,原本企業需要依靠人力抽檢的產品,現在借助工業大數據的數據建模,產品產出時即可根據實時參數判定產品是否合格,從而實現產品全檢,減少不良品的產出。
模式2:搭建全流程平臺推行個性定制
一萬個客戶一萬種想法。南京“我樂家居”通過互聯網,實現全屋家具的小批量個性化定制,給消費者帶來更好的體驗。這樣的改變,緣于該企業建立的內外全業務全流程互聯互通協作平臺。
“顧客在門店,甚至在家里,依靠互聯網,即可與我們的家居設計師共同完成對家居生活的定制。系統隨即生成符合定制櫥柜行業特點的訂單。訂單下達后,平臺即開始對訂單全生命周期的管控與追蹤,以保證顧客如期獲得滿意的成品。”“我樂家居”相關負責人李莉介紹。
與大規模標準化流水線生產相比,個性化定制往往會帶來時間與金錢的大幅增加。但“我樂家居”通過協作平臺,有效控制時間與成本。“按照產品屬性將產品歸入不同的結構進行流程處理,根據各類產品不同的交期,細化供應鏈管理流程;不同類產品在同一發貨時間的要求下,分開生產、采購、備庫,只需在發貨步驟時集中,有利于減少不同類產品間因生產周期的不同而互相等待的情況,減少產能浪費,提高供應鏈效率。”李莉說,個性化定制大大增強了企業競爭力,這幾年企業銷售增長都在30%以上。
模式3:制造企業購買專業云服務
卡特彼勒是全球著名的工程機械生產廠家,目前包括徐州工廠在內的中國廠區均擁有國內頂尖的物聯網信息平臺。在這個平臺上,企業可以實現工程機械全生命周期管理、溯源管理、預測性維護、能耗管理、產業鏈數據深度挖掘等諸多功能,從而節約成本,并為客戶提供增值服務。
這個平臺并非卡特彼勒自建,是租用的一家叫做天澤信息的企業提供的云平臺。卡特彼勒無需建設大數據中心,不必購買大量基礎軟件和應用軟件,所有的技術服務人員由天澤信息提供,而每臺裝備平均一個月的租金大約僅需幾十元。
天澤信息,是江蘇省一家專業打造工業企業物聯網和大數據公共服務平臺的高新技術企業。企業相關負責人楊美群說,除了服務卡特彼勒、徐工、日立、美的等知名大企業,公司還為數百家中小企業提供云服務,幫助這些企業走上轉型升級之路。而成立17年的天澤信息,目前已在創業板成功上市。
模式4:大企業引領產業鏈協同發展
南京先聲藥業與多家知名機構共同成立“精準醫療百家匯”項目,將成熟的研發平臺、制藥資源以及制藥工業協同云平臺開放給創業者,與他們共同成長,助推我國醫藥產業的發展和升級。
“先聲藥業百家匯平臺,集聚近百家創新創業團隊,有醫藥研發,有生物制藥,也有藥品零售企業。”企業相關負責人萬宇介紹,該平臺通過多個軟件板塊,實現制藥內外協同化的落地。一是業務計劃的協同。依靠以往業務銷售數據,各家企業協同制定生產、采購的需求與計劃。二是生產過程的協同。生產的計劃,制造,審核等全過程管理,均在流程線上處理。三是供應鏈管控的協同。上下游企業的物料配送、經銷商、藥店的發貨記錄均在系統上線,通過發貨需求能夠統籌完成對上游企業物料的采購。四是數據分析決策的協同。對以往的生產記錄、發貨記錄、物料采購記錄進行統籌分析預測,基于數據進行精準商業決策。
模式5:牽手阿里讓制造更聰明
年初,江蘇省經信委聯合阿里云組織開展“133工程”,發展工業互聯網,綜合運用新一代互聯網技術著力提升企業生產和經營能力。目前,阿里與江蘇省悅達起亞、天合光能、協鑫集團等27家重點骨干企業達成基于大數據、云計算技術的制造優化合作意向。
位于蘇州的保利協鑫光伏切片事業部,去年4月牽手阿里云,目前已在工業大數據應用上初嘗甜果。相關負責人周小棟說,借助流式數據上傳技術,公司每天有超過一億筆的數據不間斷實時上傳到云端。這些數據在云平臺自動比對標準參數運行曲線模型,就可以監控生產設備是否正常;一旦核心參數數據超過閾值,系統將通過‘釘釘’消息平臺通知現場作業人員及時響應;而通過云計算多變量處理技術,他們陸續建立生產過程故障診斷算法、核心零部件劣化預測算法、設備工藝推薦算法、良品率預測仿真算法等。
去年10月,保利協鑫切片事業部下屬一個車間在停工一段時間后復工,卻發現良品率相較其它車間始終低7%左右。技術人員依據傳統經驗花了很長時間也沒能解決,后來借助云平臺生產過程故障診斷功能,分析結果明確聚焦核心模具參數異常上。在推動上游模具供應商改善后,良品率立即提高5個百分點。