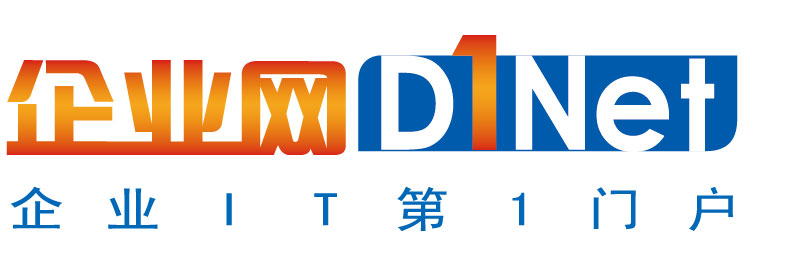
根據(jù)日經(jīng)新聞6月29日消息,多虧開發(fā)出了新的人工智能分析系統(tǒng),東芝的支柱產(chǎn)業(yè)閃存業(yè)務(wù)的生產(chǎn)效率提升,東芝有望加快逃出經(jīng)營困局。
在東芝的三重縣四日工廠,AI分析技術(shù)主要用于監(jiān)控半導體生產(chǎn)過程中的良品率,對于不合格的電路晶圓,還能發(fā)揮自動進行缺陷分類,找出原因并分析其發(fā)展趨勢等作用。
東芝三重縣四日工廠生產(chǎn)車間
一家總部位于東京的電子產(chǎn)品制造商表示,目前檢測和記錄晶圓的表面溫度和電壓仍然是技術(shù)人員在生產(chǎn)過程中的主要環(huán)節(jié),如投影曝光和拋光。而在AI分析系統(tǒng)的測試過程中,發(fā)現(xiàn)有故障的制造工藝或設(shè)備所需的時間,從過去5、6個小時減少到不超過2小時。該公司表示本財年內(nèi)也將在晶圓缺陷檢測中引入AI分析技術(shù)。
AI分析程序?qū)⑼ㄟ^引入圖像識別技術(shù)和其他技術(shù)達到深度學習的能力,這樣的系統(tǒng)將能夠自動檢測晶圓上的灰塵、不規(guī)則表面以及斑點。東芝正在不斷調(diào)試AI分析系統(tǒng)使之能適用于在其他設(shè)備的生產(chǎn)環(huán)節(jié),同時也能夠賣給其他生產(chǎn)商。
半導體領(lǐng)域技術(shù)飛速的發(fā)展著,芯片的電路密度越來越大而體積卻越來越小。通過與其他領(lǐng)域的不斷結(jié)合創(chuàng)新,半導體的制造過程變得越來越復(fù)雜,制作過程可能需要耗時三個月、包括大小2萬個步驟。正因為如此,不少企業(yè)看到了通過AI技術(shù)簡化給生產(chǎn)制造帶來了很高的自由度。
從2005年開始,索尼一直使用AI分析系統(tǒng)識別在半導體制造中缺陷產(chǎn)品及其產(chǎn)生因素。據(jù)報道,索尼長崎縣生產(chǎn)基地因為使用AI分析系統(tǒng),良品率提高了3%,一年可節(jié)約36億日圓(合3500萬美元)生產(chǎn)成本。除此之外,索尼熊本縣的圖像傳感器工廠也采用了AI系統(tǒng)。瑞薩電子則采用AI系統(tǒng)通過特殊氣體檢查的電壓來確定晶圓的表面情況,從而預(yù)測產(chǎn)品缺陷。