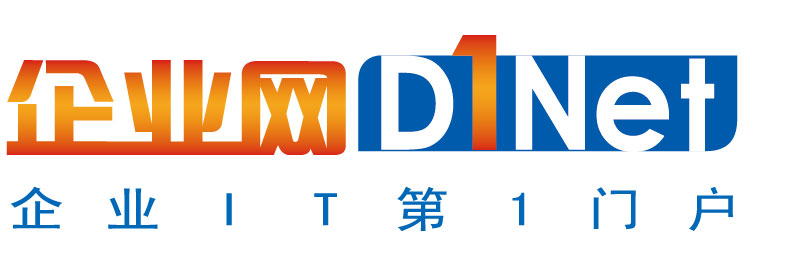
物聯網技術正在重塑整個制造業,在自動化基礎上融合新一代信息化技術,實現生產線的數字化轉型。從工廠的層面來看,萬物互聯浪潮發展簡化了設備維護的流程;從客戶服務方面來說,物聯網幫助企業實現了更全面的服務。
工業物聯網將為制造創造巨大的收入,制造商開始在自己的產品里嵌入一些傳感器來收集相關信息,包括監控產品材料、性能和在使用過程的實時信息,用來幫助企業調整產品計劃和優化產品性能。從飛機到汽車發到機和醫療設備,例如將在開發產品時將傳感器內置在零部件里,從而提升產品性能,讓產品變得更安全,可以獲得更長久的使用等。
制造商將能在問題出現前實現預測性維護,從而從根本性減少停機時間和維護成本。物聯網的使用提高了客戶的智商,新一輪以智能制造為核心的生產模式正在快速逼近。據相關機構預測,到2020年全球物聯網支出將達到700億美元。
實時診斷提升產品質量
一件產品從設計到生產再到用戶使用,其整個生命過程都處于監控和數據采集的過程。通過嵌入式傳感器和控制器可以幫助客戶發現產品潛在的問題,然后反饋給設計和生產部門,使得產品在設計、材料選型和生產過程合理避過一些誤區。同時,廠商可以通過信息收集了解客戶使用的具體情況。
通常設備廠商不知道他們設備在現場運行會發生什么事,直到用戶打電話來反饋才知道。有些廠商每隔一段時間做一次客戶調查,才能了解他們對產品使用的真實情況。除非在產品內部安裝監控傳感器,否則制造商和銷售不會意識到設備哪里出問題,只能等客戶投訴。
許多廠商有同樣的問題,對于安裝在客戶現場的產品運行情況知之甚少。而在物聯網時代,有關設備的溫度、風扇運行時間和能源消耗的信息都可以通過網絡報告給制造商,廠商可能考慮商業應用中實時診斷。
利用傳感器遠程監測
基于設備數據的接收和分析,制造商可以幫助客戶避免故障和提高機器效率。這些公司也可以收集他們的工藝的技術數據,從而調整產品和部件的設計實現更耐用和更高性能的產品方案。首先是在設計中避免問題,其次是在生產后采取糾正措施,如修理、維護或更換。
制造商可以在幾乎所有的制造工序中進行數據采集,這些數據有助于優化生產計劃安排,指引企業如何利用資源設施,讓企業更好地利用閑置設備和機器。在產品中內置傳感器,可以幫助公司實現產品離開工廠后的數據采集,通過記錄設備數據,比較設備在不同的環境下的表現,通過這些過程可以挖掘出運營效率低下的問題,從而避免了致命性失敗。
通過分析或利用數據,制造商可以進行更合適的預防性維修和保修計劃,而不是等到設備出錯時才去處理。傳感器的數據可以幫助廠商提前得到預警,確定什么是需要的維護,根據設備的性能配置合理的參數以獲得最佳性能。
遠程狀態監測(RCM)是一個基本的服務,也是影響客戶服務質量的一個重要因素。在售后服務支持中,實時訪問產品狀態信息的能力是非常有用的,特別是因為它能更有效的從根本原因分析上解決產品的問題。遠程狀態監測的下一步顯然成為預測性維護,使用傳感器如熱成像、聲波和超聲波振動分析,在問題發生之前檢測出來。物聯網為企業改善客戶服務和推動銷售量提供了一個很好的方式。
當然,工業物聯網帶來了機遇同時也有著巨大的挑戰,安全和隱私是行業關注的重要問題之一。不安全的連接設備,可能為攻擊都提供了一個后門,不但危害了消費者,也使得工業物聯網提供商蒙受損失。
從被動維修到主動維護
基于物聯網大數據的預測性維護正在逐漸流行,據分析有1/4的制造商已經通過預測性維護軟件來跟蹤產品的性能。廠家對物聯網的使用越來越感興趣,經營預測維護市場規模估計將從2015年5.8億美元增長到2020年的18.8億美元。
制造商正在整理數據從資產在價值鏈獲得見解和分析資產利用率、故障預測與提升資產壽命。例如,當資產功能的特定組件或部分最佳資產通過機器數據技術和遠程監控應用向中央系統發送所需的信息。
建立一個以客戶為導向的服務生態系統,需要廠商為其安裝基礎維護數據采集產品。在實時采集基礎信息可以大大提高價值,它們產生新的客戶以及提高售后業務和盈利能力。安裝基礎遠程監控也創造了一個可能性提供遠程服務。
最重要的是,它會產生一個新的收入來源,同時提高客戶滿意度,使制造商能夠抵消在經濟低迷時收入下降的現象。信息化解決了資產管理團隊因檢測不足而導致突然停機或故障的問題,通過物聯網將實物資產、人和流程無縫連接起來。許多制造企業都采用物聯網對生產進行監控,從而降低成本,提高安全性,制造更強大的產品和提高整體設備效率。
在物聯網時代,工廠可以實現更大的可視化生產車間,提高生產效率,增強盈利能力。預測性維護可以優化正常運行時間和計劃停機時間,客戶的訂單能及時滿足。此外,作為預測性維修計劃,需要包括使用一個中央數據庫標識備件、資產狀況和客戶訂單,跟蹤成本和確保適當的財務管理。
選擇合適的分析模型
物聯網正在成為一個強大的變革力量,它是制造企業設備維護和增強客戶體驗不可或缺的技術。而物聯網趨勢將提高復合分析模型的使用,制造商也可以選擇傳統的分析模型來實現這些目標。
傳統的分析模型區分可修復和不可修復的部分,預測設備失效的周期。這些模型利用歷史失效時間數據確定零件未來的失敗時間。在這種情況下,制造商從傳感器獲得數據詳細信息,這些模型證明特別有用。與復合模型不同的是導致零件失效也是確定因素,此功能可超出傳統的分析模型的一般特征。
對于制造商來說,接下來的問題是哪種模式更適合他們的特定需求。對此,需要考慮幾個問題。首先,數據的可用性是一個重要的因素,當數據導致零件失效和信息部分失敗事件是可用的,選擇復合模型更適合。另一方面,當只要求數據檢索,傳統的模型往往是更合適的。
其他因素影響分析的選擇是部分可修或不可修到故障預測及零件的生命周期階段完全不同。用正確的模式,制造商可以把他們的預測性維修工作的升到新水平。隨著越來越多的玩家意識到這一點,我們將在行業中看到更聰明、更高效的制造企業。