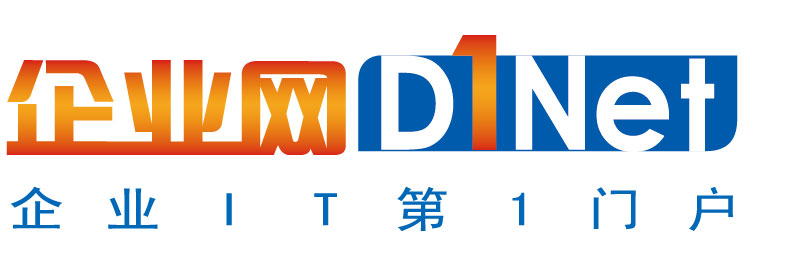
據中國網絡視聽節目服務協會發布《2019中國網絡視聽發展研究報告》顯示:2018年中國網民相比上一年平均每天增加1小時上網時間,高達5.69小時。而這每天近1/4時間里,手機掌握著出行、社交、學習、吃飯、娛樂、購物…無疑已成為現代人的生活必需品。
一臺“優秀”的手機,離不開精益求精的模具開發
其實我們所熟悉的手機,超過 60% 的部件都是模具組裝而成的,除了手機以外,還有車輛、船舶、飛機、航天器等。模具由于其塑料密度小、節能、可減輕機械設備重量等優勢,在產品生產中有非常廣泛的應用。
手機的生產離不開高質量的模具。比如,模具強韌性決定了產品的結實程度、模具原材料的密度會影響產品舒適度等。隨著現代工藝對模具質量要求越來越高,模具生產體系也就面臨著更多的挑戰。
模具開發主要分為三個階段:設計、加工與組立、試模與修善,三者缺一不可。模具設計開發工藝流程長,但制造時間要求卻很緊。
比如,注塑件往往需要與其它零部件一起配套才能組成完整的產品,但很多情況下,都是其它部件已經完成、急等注塑件配套才能上市。同時,制品的形狀或尺寸精度要求很高,而樹脂材料特性各異,因此注塑件模具制造完成后,還需要反復地試模、仿真和修正,對完美的追求使得開發和交貨時間愈加緊張。
一次高效的現代模具生產,離不開高性能的云仿真技術
通過仿真云平臺的計算仿真和模擬技術,可以對產品進行設計、改進、創新,以及模型的快速認證和方案的快速對比,不但解決了大量零散復雜的仿真數據可控性差的問題,還在安全性、耐久性、一致性方面得到保障。
使用高性能云仿真服務的模具制造企業,不管是加快產品研發,還是滿足企業日益增長的模具仿真需求,亦或是提高 IT 投資回報率,都會得到立竿見影的效果。
聯合在模具設計、仿真方面有先進經驗的軟件服務商,華為云 FusionPlant 研發協同平臺為模具企業提供高性能、高可靠、可快速部署、簡便安全的設計、仿真解決方案,幫助企業實現降本增效。
華為云仿真的最佳實踐——東江集團研發設計平臺
東江集團是一家全球領先的一站式注塑解決方案供應商,致力于精密電子類、高精密高性能的模具(如汽車類模具、及其他大型復雜模具)的研發、設計與制造。隨著東江的業務不斷壯大,原有的仿真平臺效率滿足不了東江集團的業務需求,工程師大部分時間都浪費在等待仿真結果的過程中,極大提高人力消耗和拖慢項目交付。
東江集團攜手華為云后,應用華為云FusionPlant研發的設計平臺進行模具注模的仿真,實現仿真計算資源統一調度。
實驗對比結果顯示:進行復雜模型仿真時,效率提升 97%,由之前的 123 小時減少到 3 小時;進行簡單模型仿真時,效率提升20%,由之前的 12 小時減少至 10 小時。除此之外,東江集團選擇華為云,不僅源于華為云 FusionPlant 仿真平臺生態豐富、快速部署、超高性能等優勢,更是因為其完備的數據安全保障能力。
當進行仿真計算時,特別是一些大型的仿真項目會生成海量的數據,企業要將仿真應用交付到云端,必然要考慮安全性。華為云仿真平臺提供端到端的安全解決方案,保證用戶數據不泄露,讓東江集團無后顧之憂。
不僅是手機,模具在日常消費電子類產品、家電產品、汽車行業等都有廣泛的應用。華為云FusionPlant提供的高性能、高可靠、簡便安全的仿真服務,將致力滿足工業制造中零部件等仿真需求,幫助模具企業鑄造工業互聯網數字基礎,讓高質量的模具打造的高品質產品走進千家萬戶。